To Convert Or Not to Convert?
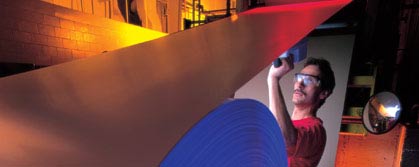
Outsourcing vs. In-House – the Numbers Don't Lie.
If you fabricate sheet metal into parts or products and then paint them for decoration or corrosion resistance, you need to consider the substantial savings possible by converting from an in-house paint operation to prepainted metals.
Switching to prepainted metals can increase quality, improve productivity and remove costs that drag down profits. But timing, capital outlay, manufacturing costs and environmental compliance should all play a part in the decision. Here's an in-depth look at how the pros and cons add up.
Timing is Everything.
The best time to consider making the change to prepaint is in conjunction or coordination with other milestone events in your business.
Do you need to cut costs to stay more competitive on price?
Getting rid of an in-house postpaint operation can help you do that and improve quality at the same time – which could be the one-two punch that knocks your competition out.
Have you already decided to downsize or combine plants?
You’ll eliminate duplicate postpaint operations plus maximize floor and ceiling space by removing your in-house operation completely and switching to prepainted metal.
Already leaning toward an outsourcing strategy?
If your competition keeps you from raising price, outsourcing to prepainted metals could be the best way to remove cost from your operation.
Are major capital improvements already planned?
Make switching to prepainted metal a part of improvements now and reap major results in the future.
Has the EPA become a major P-A-I-N?
As regulations get stricter, the cost of meeting them gets higher – working with prepainted metal gets rid of all those headaches.
Make Sure You Measure All the Costs.
It pays to consider all the hidden costs of your in-house operation.
Inventory: Paints, chemicals, solvents, cleaners, applicators, work-in-progress, bare parts, pretreated parts, primed parts, painted parts
Environmental: Clean-up programs, legal actions, compliance programs, fines and penalties
Insurance: Coverage for your part finishing area, toxic premiums
Cleaning/Waste Treatment Removal: Sludge removal, clean-up, cleaning supplies, cleaning tasks, maintenance
Floor & Ceiling Space: Cleaning equipment, rework stations, pretreating equipment, priming equipment, painting equipment, work-in-progress conveyors
Purchasing: Sourcing, order follow-up, status reporting, negotiating specs & prices, standard cost development, purchase orders, damaged goods, stocking programs
Operating Costs: Energy, filters, delays, rejects, equipment maintenance, lubricants, shutdowns, rework, spare parts
Finishing & Cleaning Material Handling: Receiving, requisitioning, cycle planning, preventive maintenance, inspecting, spoilage, disposition, maintenance.
Almost as Simple as 1-2-3.
Anything as monumental as eliminating your in-house postpaint operation won’t be quick and easy. But the step-by-step process of deciding whether to go to the next level of assembling a conversion team for detailed review can be amazingly direct and take just three steps:
- Measure the actual costs (hidden and otherwise) associated with post-painting and its support functions.
- Total the money saved (hard costs plus compliance) by eliminating post-painting process.
- Subtract the increased raw material costs of using pre-painted metal and chances are you’ll find yourself on the winning side of this equation ... by far!